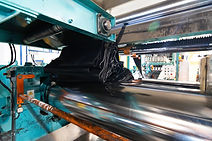
Molding & Fabrication - ERP Solution
A constant challenge for injection molding, foam fabrication, woodworking, furniture building or any similar facilities is that they purchase & process dimensional raw materials through multiple operations that alter their physical sizes.
The ability to track materials like offcuts & drops, while desirable, is easier said than done when it's a manual process and the right mechanisms aren't in place to do so.
Epicor has always been good in the “dimensional inventory” space, but with their more recent releases, Epicor has elevated this specialty to a new level with their metal fabrication industry ERP product.
Sheet metal, plastic fabrication, etc., are all industries that rely on the continuous reforming of materials, even regrinds. Epicor Kinetic can not only tackle the challenges that these companies face, but it can also help streamline these processes, as well.
Key ERP System Functionality for Molding & Fabrication
Ancillary Devices & Tooling Management
-
Scheduling and Maintenance: Kinetic can schedule ancillary devices like anilox rolls and unwind spools, ensuring they are maintained properly.
-
Resource Optimization: Helps manage the availability of critical tooling, preventing production delays.
-
Investment Management: Tracks the lifespan and usage of ancillary tools to maximize their value.
-
Operational Efficiency: Schedules tools effectively to ensure smoother and more efficient operations.
-
Capacity Planning: Manages limited tooling resources to optimize job scheduling and prevent bottlenecks.
Materials Manipulation & Nesting
-
Integrated Material Handling: Kinetic handles materials manipulation without relying on external systems, ensuring smooth operations.
-
Trim Utilization: Tracks and uses trim materials as raw materials for other production needs, reducing waste.
-
Nesting Program Integration: Interfaces with major nesting programs to streamline data transition and production processes.
-
Automated Setup: Automates the setup and posting of nested products, enhancing efficiency.
-
Accurate Scheduling: Calculates production times based on cutting speed and part dimensions for precise scheduling.
Mold & Die Management
-
Usage Tracking: Monitors the total usage of molds and dies to schedule preventive maintenance and extend tool life.
-
Performance Monitoring: Tracks takt time and machine metrics to detect premature wear and operational issues.
-
Cost Management: Records original and subsequent rebuilding costs for accurate financial tracking and depreciation.
-
Real-Time Alerts: Provides alerts for potential issues affecting tool life, ensuring timely interventions.
-
Lifecycle Management: Ensures proper management of molds and dies to avoid premature scrapping or rebuilding.
Recycling & Resource Management
-
Waste Monitoring: Tracks waste production and regrinds for reuse in other products, minimizing virgin material needs.
-
Co-Parts Management: Manages ‘co-parts’ production from molds producing multiple parts or theoretical scrap.
-
Supply Chain Optimization: Enhances material management to address supply chain issues and ensure resource availability.
-
Sustainability Initiatives: Supports recycling efforts to conserve resources and promote sustainability.
-
Resource Tracking: Monitors and utilizes waste as raw materials for new products, improving overall material efficiency.